2023-09-01
The process of RTM is a manual one, which can involve almost any reinforcing material. The process requires a core, cavity, and tools, which can be made of composite materials, aluminum, or stainless steel. As a result, the resin-infused part has excellent surface finishes. In some cases, a gel coat is injected into the mould cavity to improve the finish. This creates a paint-ready surface.
The RTM process consists of five distinct phases. Rotec moulds are made of aluminium or steel. The glass reinforcement is placed in layers within the open mould. Each layer has a predetermined size, weight and shape. The closed mould is clamped by a hydraulic press. High-pressure injection and high-temperature curing cure the resin inside the mold. Once the resin is inside, the mould is ready for injection.
The RTM process uses closed moulds to force the resin into the cavity. Depending on the requirements, the moulds can be made of steel, aluminum, or other materials. During the second phase, the mould is closed and layers of pre-cut fiberglass reinforcement are placed inside. Each layer is pre-cut and pre-determined for each product. Finally, a hydraulic press applies clamping force to the closed mould. The resin is injected by a high-pressure injection, and the mould is cured by applying heat.
The RTM process is a manual process. It allows the use of almost any type of reinforcing material. The RTM process uses a variety of types of tools, including metal and composite materials. The finished parts from this process have extremely good surface finishes and are perfect for paint applications. The RTM process can be automated, as well as fully manual. Regardless of the procedure, the RTM process can be a highly productive and cost-effective way to manufacture a wide variety of products.
A custom RTM mould is a critical part of the production process. A quality RTM mould is the foundation of your manufacturing operation. With a well-designed custom RTM mould, you can produce parts that are highly durable and aesthetically pleasing. The RTM process also helps control the emissions of styrene. In addition, the RTM process can reduce the cost of raw materials, which allows your business to grow.
Custom RTM moulds are an essential part of RTM manufacturing. The process involves inserting a composite preform into a metal mould, which is then filled with liquid resin. This process is also useful for the co-curing of foam, metallic inserts, and pre-cured details. Infusion RTM moulds are highly customizable and customized to the needs of your company. They can be customized to meet the exact specifications of your products, and can be molded from any material, including plastics and wood.
There are several different types of RTM moulds. Infusion moulds are used for high-volume production, while contact moulds are used for medium-volume parts. The RTM tools are made from matched metal tools. The resin is poured into the mould cavity after the preform is inserted. When the resin is cured, it is able to be removed. If you need more complex RTM moulds, consider contacting an experienced mold maker.
The process of RTM is a complex one. For this reason, a custom RTM mould is an invaluable tool for any company. It allows you to manufacture complex parts in a controlled environment. By using a steel or aluminium mould, RTM moulds can be customised to meet your exact specifications. They can also be modified to fit specific components. By following the instructions, you can achieve the highest level of precision possible.
The RTM process uses aluminium or steel moulds to form a composite part. Once the resin is poured, it consolidates the preform into a mould. Afterwards, the part is cured by applying a hydrostatic pressure. These two processes are different, and there are many advantages to each. It allows for excellent dimensional control and can be used for co-curing foam, metallic inserts and pre-cured details.
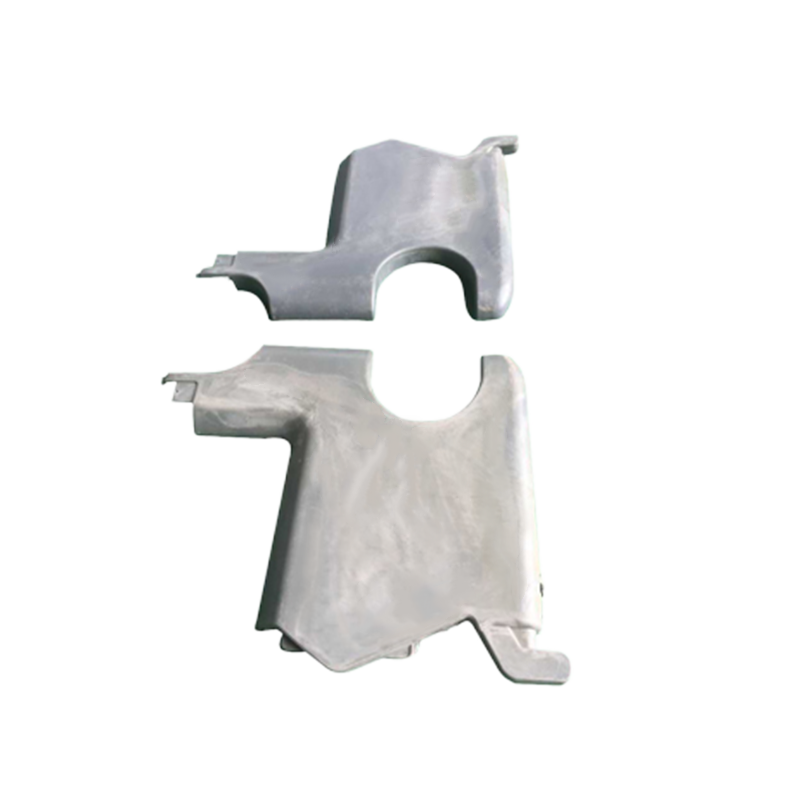